Die-Cast Terms & Definitions (Reference Aid Only - Uncontrolled)
Aging
A change in the metallurgical structure of an alloy occurring over a period of time following casting, which affects the properties and dimensions. Heating accelerates aging.
Coat Rack Tree
Alloy
A substance having metallic properties and composed of two or more chemical elements, of which at least one is metal. Alloy properties are usually different from those of alloying elements.
Anode
The electrode in a plating bath at which metal ions are formed, negative ions are discharged, or other oxidizing reactions occur.
Anodic Metal
Any metal that tends to dissolve, corrode, or oxidize in preference to another metal when the metals are connected electrically in the presence of electrolyte.
Anodizing
To subject a metal to electrolytic action as the anode of a cell in order to coat with a protective or decorative film.
As Cast
Condition of a casting that has not received finishing (beyond gate removal or sandblasting) or treatment of any kind including heat treatment after casting.
Atmospheric Corrosion
Surface corrosion caused by exposure to gasses or liquids that attack the metal.
Barrel Plating
Plating in which the work is processed in bulk in rotating container.
BHN
Brinell Hardness Number
Biscuit
Excess metal left at the end of injection cylinder of a cold chamber machine, formed at the end of the plunger stroke, also called a slug.
Blister
A surface defect or eruption caused by expansion of gas, usually as a result of heating trapped gas within the casting, or under metal plated on the casting.
Blow Holes
Voids or holes that may occur due to entrapped air or shrinkage during solidification of heavy sections.
Bright Finish
A finish with a uniform non-directional smooth surface of high secular reflectance.
Buffing
The smoothing of a surface by means of a rotating flexible when the surface of which fine abrasive particles are applied in liquid suspension sion, paste, or grease-stick form.
Cass Test
(Copper accelerated salt spray) An accelerated corrosion test for electroplated substrates (&_STM 369-68)
Casting Yield
The weight of casting or castings divided by the total weight of metal injected into the die, expressed as a percent.
Cathode
The electrode in the electroplating at which metallic ions are discharged, negative ions are formed, or other reducing actions occur.
Cathode Robber
An auxiliary cathode so placed as to divert electrical current to itself from portions of the articles being plated which would otherwise receive too high a current density.
Cathodic Metal
Any metal that does not tend to dissolve, corrode, or o daze in preference to another metal when the metals are connected electrically in the presence of an electrolyte.
Cavity
The recess in the die in which the casting is formed.
Charpy
Name of an impact test in which the specimen, forming a simpt beam, is struck by a hammer while resting against anvil supports spaced mm apart.
Checking
Heat-crazing of a die surface, especially when subjected to repeated heating by molten alloys at high casting temperatures. The resulting fine cracks produce corresponding raised veins on die castings.
Chromate
A conversion coating consisting of trivalent and hexavalent chromium compounds.
Chromating
The application of chromate coating.
Chrome Pickle
A chemical treatment for magnesium in nitric acid, sodium dichromate solution. The treatment gives some protection against corrosion by producing a film that is also a base for paint.
Cold-Chamber Machine
A die casting machine arranged so that the me chamber and plunger are not immersed in molten metal.
Coldshut
A lapping of solidified metal that sometimes occurs in the formation of die castings which constitutes an imperfection or near the s face of the casting.
Combination die
A die with two or more different cavities each producing a different part.
Composite Plate
An electro-deposit consisting of two or more layers of metal deposited successively.
Compressive Yield Strength
The maximum stress that a metal, subjected to compression, can withstand without a predefined amount of yield. (normal 0.2% of die castings).
Contraction (Shrinkage)
Tile volume typically occurring in metals and alloys on solidification and cooling room temperature. Cooling channel See Water line.
Core Pin
A core, usually of circular section. Core pins may be fixed or movable.
Core Plate
The plate to which the cores are attached and which actuates them.
Kesternich
An accelerated corrosion test for electroplated substrates (ASTM 380-65).
Corrosion
Destruction of a metal by chemical or electrochemical reaction with its environment.
Corrosion Endurance
Resistance to corrosion as a function of time.
Cover, Cover Die
The stationary half of a die casting die which forms the exterior or appearance surfaces of the casting.
Cover Gas
A mixture consisting of sulfur hexafluoride, carbon dioxide and air, used to protect and minimize oxide formation on the surface of molten magnesium.
Creep Plastic
Deformation of metals held for long periods under stresses less than the normal yield strength.
Creep Strength
The constant nominal stress that will cause a specified amount of creep in a given time at a constant temperature.
Current Shield
A non-conducting medium for altering the current distribution on an anode or cathode.
Damping
Ability of material to dampen vibration in components and thus lower noise levels.
Deburring
The removal of burrs, sharp edges, or fins by mechanical, electrochemical or electrical discharge means.
Dendrite
A crystal that has a tree-like branching pattern most evident in cast metals slowly cooled through the solidification range.
Dichromate Process
A chemical treatment for aluminum, magnesium and inc alloys in a boiling dichromate solution, resulting in a surface film that resists corrosion.
Die
A metal block used in the die casting process, incorporating the cavity or cavities that form the component, the molten metal distribution system, and means for cooling and ejecting the casting.
Die Casting
The metal on the surface of a die casting, to a depth of approximately.020 in. (o.8mm), characterized by fine grain structure and freedom from porosity.
Die Insert
A removable liner or part of a die body.
Die or Steel Safe
A technique employed in close-tolerance die casting in which exterior surfaces of the casting are deliberately made slightly under size, and the interior surfaces slightly over size. After a trial casting run, all dimensions are brought within specified tolerances. This technique ensures that all final die modifications, no matter how slight, are made by removing, rather than adding metal.
Dimensional Stability
Ability of an alloy to retain its size and shape unchanged with time.
Dolomite
A mineral made up of calcium and magnesium carbonate.
Dowel Pin
A guide to ensure registry between two die sections.
Draft
A taper given to cores and other parts of the die cavity to permit easy ejection of the casting.
Drag-Out
The solution that adheres to the objects removed from cleaning and plating baths.
Dross
Metal oxides in or on the surface of molten metal.
Dull Finish
A finish virtually lacking both diffuse and secular reflectance
Ejector, Ejector Die
The movable half of a die casting die containing the ejector pins; this half forms the interior or non-appearance surfaces of the casting.
Ejector Marks
Marks left on castings by ejector pins, frequently including a light collar of flash formed around the pin.
Ejector Pin
A pin actuated to fore the casting out of the die cavity and off the cores.
Ejector Plate
The plate to which the ejector pins are attached and which actuates them.
Electrolyte
A substance, usually liquid, in which the conduction of electricity is accompanied by chemical decomposition. An electrolyte is one of the factors required for electrolytic corrosion to occur.
Electromotive Series
A list of elements arranged according to their standard electrode potential.
Electroplate
An adherent metallic coating applied by electro-deposition on a substrate for the purpose of improving the surface properties.
Fatigue
The phenomenon leading to fracture Linder repeated or fluctuating stresses that have a maximum value less than the tensile strength of the material.
Feeding
The process of supplying molten metal to the die cavity to compensate for volume shrinkage while the casting is solidifying.
Fillet
Curved juncture of two surfaces; e.g., walls that would otherwise meet at a sharp corner.
Flash
The thin web or fin of metal on a casting occurring at die partings, air vents, and around movable cores. The excess metal is due to the working pressure and operating clearances in the die.
Flux
A substance such as Halide salts used to protect and minimize oxide formation on the surface of molten metal. Also used to refine scrap metals.
Fracture Test
Breaking a specimen and examining the fractured surface. -To determine such things as composition, grain size, soundness, or presence of defects.
Galling
Tearing out of particles from a metal surface by sliding friction.
Galvanic Corrosion
Corrosion associated with the current of a galvanic cell consisting of two dissimilar conductors in an electrolyte or two similar conductors in dissimilar electrolytes.
Gate
The passage connecting a runner or overflow with a die cavity. Also, the entire ejected content of a die, including the casting or castings and the gates, runners, spur (or biscuit) and flash.
Gooseneck
In hot-chamber die casting, a spout connecting a metal pot or chamber with a nozzle or spur hole in the die and containing passage through which molten metal is forced on its way to the die.
Growth
Expansion of a casting as a result of aging, intergranular corrosion, or both.
Hardware Finish
An especially smooth, as-cast surface requiring no polishing and little buffing in preparation for plating.
Hardware Finish
An especially smooth, as-cast surface requiring no polishing and little buffing in preparation for plating.
Heat Checking
See Checking.
Hot-Chamber Machine
A die casting machine arranged with the metal chamber and plunger immersed in the molten metal.
Hot Short
Brittle or lacking strength at elevated temperatures.
Hot Tear
A rupture occurring in a casting at or just below the solidifying temperature by a pulling apart of the soft metal, caused by thermal contraction stress.
Impact Strength
Ability to resist shock, as measured by a suitable testing machine.
Impression
A cavity in a die. Also, the mark or recess left by the ball or penetrator of a hardness tester.
In-gate
The passage or aperture connecting a runner with a die cavity.
Ingot
A pig or slab of metal or alloy.
Injection
The act or process of forcing molten metal into a die.
Insert
A piece of solid material, usually metal, that becomes an integral part of the casting. Inserts are commonly set in the die so that metal is cast around that portion left exposed in the die cavity. Alternatively, inserts are often applied subsequent to casting. (Note: inserts become a part of the casting, whereas die inserts are a part of the die.)
Intergranular Corrosion
A type of corrosion that preferentially attacks the grain boundaries of a metal or alloy resulting in deep penetration.
Izod
Name of an impact test arid testing machine in which the specimen is clamped at one end only and acts as cantilever beam when struck by the hammer.
Knockout, Loose Piece
A core position by the riot fastened to a die and so arranged as to be ejected with the casting. The knockout is subsequently removed and used repeatedly.
KIS
PSI (pounds per square inch) expressed in thousands.
Leveling Electroplate
An electroplate that produces a surface smoother than the substrate.
Metal Distribution Ratio
The ratio of the thickness of metal upon two specified areas of a cathode. (See Throwing Power.)
Metal Saver
A core used primarily to reduce the amount of metal in the casting and to avoid sections of excessive thickness.
Microthrowing Power
The ability of a plating solution or specified set of plating conditions to deposit metal in fissures, pores, or scratches.
Miniature Die casting
Die cast processing on specialized hot-chamber machines which can produce very small complex parts, from a fraction of an ounce up to 16 ozs, to net shape and flash free, requiring no trimming operation.
Multiple-Cavity Die
A die having more than one duplicate cavity.
Net Casting Yield
See Casting Yield
Nozzle
The outlet end of a gooseneck or the tubular fitting that joins the gooseneck to the spur hole.
Overflow
A recess in a die, connected to a die cavity by a gate, remote from the entrance gate (ingate).
Overflow Gate
A passage or aperture connecting a die cavity to an overflow.
Overflow Well
A recess in a die connected to a (lie cavity by a runner to assist in proper venting).
Parting Line
The join between the cover and ejector portions of the die or mold. Also the mark left on the casting at the die joint.
Pickling
Removing surface oxides by chemical or electrochemical reaction.
Pin
A core usually circular section normally having some taper (draft). Also a dowel (or guide pin) to ensure registry between two die sections.
Pitting
The appearance of small depressions or cavities produced during solidification or corrosion.
Platen
Portion of a casting machine against which die sections are fastened, or of presses against which trim dies are fastened.
Plating Rack
A frame for suspending and carrying current to articles during plating operations.
Plunger
Ram or piston that forces molten metal into a die.
Polishing
The smoothing of a metal surface by means of the action of abrasive particles attached by adhesive to the surface of wheels or endless belts usually driven at high speed.
Porosity
Voids or pores, commonly resulting from solidification shrinkage, air (primarily the nitrogen component of air) trapped in a casting, or hydrogen exuded during electroplating.
Port
Opening through which molten metal enters the injection cylinder of a hot-chamber machine or is ladled into the injection cylinder of a cold chamber machine.
Pouring Slot
Port through which molten metal is ladled into the cold chamber of a casting machine.
Rapid Prototyping (RP)
A range of processes by which prototypes are built by machine, usually in a special plastic resin, using equipment interfacing directly with CAD data. Includes the following process names: sterolithography, soldier processing, selective laser sintering, laminated object manufacturing, and fused deposition modeling.
Refine
In magnesium melting pratice, the removal of magnesium oxide and other suspended non-metallic matter by use of flux that preferentially wets the impurities and carries them to the bottom of the pot as slude.
Remelt
Sprues, gates, runners, and defective casting returned directly to the melting pot.
Robber
See Cathode robber.
Runner
A die passage connecting tile sprue hole or plunger hole of a to the gate or gates where molten metal enters the cavity or cavities.
Runaround Scrap
See Remelt.
Salt Fog Test
An accelerated corrosion test in which specimens are exposed to a fine mist of a solution usually containing sodium chloride.
Satin Finish
A surface finish that behaves as a diffuse, reflector, which is lustrous but not mirror-like.
Segregation
Non-uniform distribution of alloying elements, impurities, microstructures.
Semi-Solid Metal Casting
Casting process using semi-solid raw material with relatively slow ingate veloctieis, minimum turbulence and high pressure throughout solidifcation to produce high-integrity castings capable solution heat treatment.
Shot
A die filling or part of the casting cycle in which molten metal is forced into the die.
Shrinkage
The total reduction in dimensions of a casting from the mol liquid to room temperature.
Shrinkage, Solidification
Dimensional reduction that accompanised the freezing (solidification ) of metal in passing from the molten to tile solid state.
Shrink Mark
A surface depression, often called a shadow mark that sometimes occurs at a thick section that cools more slowly than adjacent sections.
Slide
Portion of a die generally arranged to move parallel to the partin line. The inner end forms a part of the die cavitiy wall and sometimes includes a core or cores.
Soldering
Sticking or adhering of molten metal to portions of the die.
Split Gate
A gate of castings having the sprue axis or plunger axis in the die parting line.
Sprue
Metal that fills the conical passage (spur hole) that connects the nozzle or hot chamber to the runners of a hot-chamber die casting machine. (Most cold-chamber machines form a slug and have no sprue.)
Spruepin
A tapered pin with rounded end projecting into a sprue hole and acting as a core to keep the casting in the ejector portion of the die.
Squeeze Casting
Casting process using molten metal with relatively slow in-gate velocities, minimum turbulence and high pressure throughout solidification to produce high-integrity castings capable of solution heat treatment.
Standards
NADCA Product Revised specifications, published by the Die Casting Development Council of the North American Die Casting Assn, detailing dimensional variations that should be considered in designing die castings, many expressed as "Standard" and "Precision" product tolerances.
Stress Corrosion Cracking
Crackin due to the combined effects of stress and corrosion. Usually this type of failure occurs as a fine hairline crack that propagates across the section without any exterior sign of corrosion.
Substrate
Material upon which coatings are deposited.
Sufur Hexafluoride (SFG)
A gas used in low concentrations (usually less than 1%) with carbon dioxide and air to form a protective atmosphere over the surface of molten magnesium to minimize burning and oxide formation.
Surface Treatment
A general term denoting a treatment involving a modification of tile surface.
Tensile Yield Stress
The stress at which a material exhibit's a specified deviation from proportionality of stress and strain. An offset of 0.2% is used for die casting alloys.
Throwing Power
The improvement of the coating distribution over tiloe primary current distribution on the cathode in a vigen solution under specified conditions.
The Bar, Tie Rod
A bar used in a die casting machine to hold dies locked against pressure and in general also serving as a way along which the movable die platen slides.
Tolerance Limit
The specified critical amount of an impurity element which if exceeded results in degradation of material properties.
Trim Die
Die for shearing or shaving flash from a casting. Either the die is forced over the casting, or the casting is forced through the die.
Undercut
A recess in the sidewall or core hole of a casting so disposed that a slide or special form of core such as a knockout is required to permit ejection of the casting from the die.
Special Price!!! Cherry Finish Wood Coat Rack
Nov 08, 2011 19:19:21
Click for larger image and other views
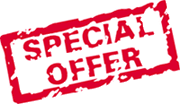
Cherry Finish Wood Coat Rack Feature
- Some assembly may be required. Please see product details.
Cherry Finish Wood Coat Rack Overview
Coat rack in cherry finish, beautiful carved with great detailing. Six hangers and triple pedestal is described best by the stylish design and the great craft. Lowest factory direct price guarantee.SAVE NOW on the special offers below!
Available In Stock. |
This Cherry Finish Wood Coat Rack ships for FREE with Super Saver Shipping. |
Price : Click to Check Update Prices Please. |
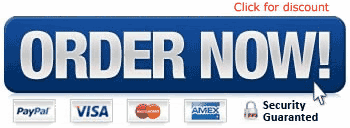
Limited Offer Today!! Cherry Finish Wood Coat Rack Black Friday and Cyber Monday Deals
Bedside Tray Tables Lightweight Tripods Amisco Counter Stools